Hogyan készül a vasúti betonalj? - Riport Lábatlanból
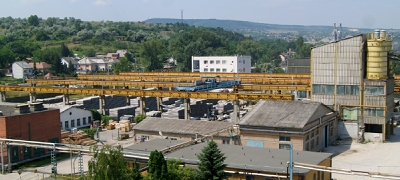
A lábatlani gyárat 1942-ben alapította kilenc részvényes kétszázötvenezer pengő alaptőkével. A vállalat fő profilja a kezdetektől fogva az előre gyártott mélyépítési vasbeton elemek, illetve a vasúti aljak voltak. Az üzemet 1948-ban államosították, ezt átszervezések, összevonások, majd tevékenység-leválasztások követték. A kisvasúti betonaljak gyártása 1949-ben, az előfeszített vasbeton aljaké 1958-ban indult meg. 1964-től mezőgazdasági, 1966-tól pedig már építőipari termékek is készülnek Lábatlanban, majd európai viszonylatban is az elsők között, 1984-ben kezdődött a vasúti kitérő és átmeneti aljak gyártása.
Negyvenöt év állami tulajdonlás után a vállalatot privatizálták, rá egy évre pedig megkezdődött a pörgetett beton technológia bevezetése. Azóta a vállalat folyamatosan fejlődik, termékpalettája bővül. 1996-tól áttört gerincű vasbeton oszlopokat, 1999-től pedig térburkoló köveket is előállít, széles választékban. A Lábatlani Vasbetonipari Zrt. 1997 óta rendelkezik a minőségirányítás ISO9001-es tanúsítványával. A vállalat három, közlekedési elemek, oszlopok és lakossági termékek divízióját 2003-ban hozták létre, és 2007-től az új, saját fejlesztésű UAB vasúti útátjáró elemek is megtalálhatóak a kínálatban. A cég többségi tulajdonosa az Európa-szerte ismert és elismert Rail.One GmbH, a kötöttpályás közlekedési vasbeton termékek egyik vezető gyártója.
A vasúti betonaljak megszületése, fejlődése egy sok évtizeden át tartó, szerteágazó történet. A három nagy korszak, az 1900-as évek első évtizedeinek kísérletezése, az 1950-ig tartó lágyvasbetétes aljak kora, és a napjainkban is főszereplő feszített betonaljak története annak terjedelme miatt egy külön cikket érdemelne, terveink szerint a későbbiekben erre is sor kerül.
A fa- és vasaljakkal szemben a betonaljak előnye, hogy teherbírásuk és tömegük nagy, előállítási költségük pedig kicsi, valamint élettartamuk hosszú, 50-70 év, ezért a vasutak előszeretettel alkalmazzák. Hazánkban új építéskor csak betonaljak, fenntartás során körülbelül fele-fele arányban fa- és betonaljak kerülnek a pályába. További előnye a betonaljaknak, hogy míg a faaljakat az utóbbi években a magyar vasút importból volt kénytelen beszerezni, a betonaljakat itthon, a Lábatlani Vasbetonipari Zrt. üzemében állítják elő.
Beton. Az építőipar, és a hétköznapok szürke eminenciása. Minden nap találkozunk vele, mégis alig vesszük észre. Betonból vannak a közvilágítás és az elektromos hálózat oszlopai, a fa póznák gyámjai, beton lábunk alatt a térkő, a házunk alapja, áthidalói vagy födémgerendái. De jelen van a mezőgazdaságban is, silók, etetővályúk, taposórácsok formájában. Készülnek itt moduláris vasbeton ipari kerítéselemek is, melyek előnye a dróthálóval szemben, hogy nem enged betekintést a gyárterületre a kíváncsi szemeknek, és illetéktelen személyek számára a kerítés megbontását is nehezebbé teszi. Ezek a termékek mind-mind megtalálhatóak a vállalat kínálatában, csakúgy, mint a többfajta transzportbeton. A gyár másik végében, egy új csarnokban térkövek, és szegélyelemek gyártása folyik. Itt az egész folyamat gépesített, csak a kész raklapokra húzott zsugorfóliát melegítik kézzel. De jelen írás fő témája nem ez, hanem a vasúti aljak előállítása. Lássuk, miből is áll ez a folyamat!
Mint minden betonterméknek, a vasúti aljaknak is a sóder az alapja. A lábatlani gyár közvetlenül a Duna partján fekszik, a kavicsot kotróhajóval termelik ki a mederből. A depóból szerteágazó szalagsorok indulnak, és szállítják a kavicsot a rostáló, osztályozó, és törőgépekhez, hiszen a különféle betontermékek előállításához eltérő szemcsenagyságú anyagra van szükség. Betonaljak gyártásakor a szalagsor a partról az osztályozóba, onnét az éppen szükséges anyagot a keverőépületbe szállítja. A keverőben két hatalmas, digitális mérlegekkel ellátott mixer található. A sódert a felsőbb szintről egyszerűen leöntik a keverőbe, míg a cementet egy csigamenet szállítja. A sóder, cement, víz és egyéb, kötést késleltető vagy éppen gyorsító vegyszerek adagolása számítógéppel történik, hogy a beton pontosan a kívánt minőségű legyen. Jelenleg a vasúti aljakat C50/60 minőségű, C10-16 földnedves, és C10-16 képlékeny öntömörödő betonból állítják elő. Ha a keverék elkészült, egy kocsiba ürítik, mely átszállítja azt a szomszédos gyártócsarnokba.
A gyártócsarnokban görgősorokon hosszirányba, láncpályákon keresztirányba mozognak az öntőformák, az éppen soron következő munkafolyamat helyszínére. Egy sablonból két sorban általában nyolc-tíz darab alj kerül ki, ez függ az alj típusától, hosszától. Mivel a betonaljak felső fele formázott, míg alsó fele sík, ezért a sablonban az aljak fejen állva kerülnek leöntésre, és csak a gyártás legvégén, a sablonból kidöntéskor állnak talpra. A gyártás a sablon szempontjából körfolyamat: Először is a fémből készült öntőformát kitisztítják, és egy speciális olajjal kenik ki, hogy később a már majdnem megkötött aljakat könnyen, a forma és az aljak roncsolása nélkül ki lehessen emelni. Ezután a sablon a „drótozóba” kerül.
Itt szintén gépi vezérléssel kerülnek lecsévélésre a kívánt hosszúságú, csavart bordás betonacél szálak, melyet a következő munkahelyen befűznek a sablon végein kialakított lyukakba. Itt kerülnek fel a kengyelek is, illetve az egyéb szerelvények: a műanyag csavarbetétek, illetve az egyes aljakat elválasztó lapocskák. Mikor a sablont „beszerelték”, azaz minden szükséges elem a helyére került, a formát a görgősor a következő munkahelyre, a „feszítőbe” szállítja. Itt egy hidraulikus pisztoly segítségével feszítik meg az acélszálakat. Ez a folyamat, az előfeszítés, mikor az acélt még a beton beöntése előtt feszítik meg, a gyártás egyik legfontosabb lépése. Ettől eltérő eljárás az utófeszítés, ahol a már megkötött aljban, az előre kialakított lyukakban feszítik meg az acélszálat. Az utófeszített aljak gyártása körülményes, és műszaki tulajdonságaik is kedvezőtlenebbek.
Visszatérve a gyártáshoz: a feszítés után a forma két végébe acéllemezeket helyeznek, hogy az esetlegesen elpattanó acélszálak ne okozhassanak balesetet. A sablont ismét görgők továbbítják, ezúttal már a betonozóba. Itt a sablon fölé áll a korábban már említett kocsi, mely a keverőből hozza a frissen bekevert betont. Kézzel mozgatva a kocsit, végigöntik a formát, miközben a vibrációs tömörítők hatalmas zajjal tömörítik a sablonba öntött betont.
A következő munkahelyre érve a sablon végigért a csarnokon. Itt kiszedik belőle az elválasztó és a csavarbetétek nyílásait kitöltő elemeket, majd a formát daru segítségével egy gőzölő medencébe helyezik. A gőzölésnek, és az adalékanyagoknak köszönhetően a beton kötési ideje hat–nyolc órára csökken.
Mikor a betonaljak megkötöttek, a daru kiemeli a formát a gőzölő medencéből, és visszahelyezi a görgősorra. A formát a borítógép oldalra fordítja, és a betonaljak kifordulnak belőle, immáron a talpukra érkezve.
A sablon visszakerül az első munkahelyre ahol kitisztítják, az aljak pedig a görgőkön hosszú sorban vándorolnak a fűrészhez „kézen fogva”, ahol a gyártás egyik utolsó műveletét végzik el. Az aljak között elvágják az acélszálakat. Ekkortól kezdve válnak egyesével kezelhetővé, tehát mondhatjuk, hogy ezzel el is készültek a betonaljak. Van, ami már így szállításra kész, de ha a megrendelő kéri, akkor az aljakat felszerelvényezik. Felkerülnek rá az alátétlemezek, és a sínlekötés elemei.
Ha az aljak elkészültek, teherautóra vagy vasúti kocsikra rakják, majd kiszállítják a megrendelőhöz. Végül a kész aljak kétféleképpen kerülhetnek beépítésre: vagy egyénileg, szórványos aljcsere keretében, vagy pedig tömegesen, kötőtelepről, gépesített vágányfektetés során. Nálunk jelenleg a celldömölki, városföldi, és esetenként a komáromi kötőtelep üzemel.
A végére pedig egy vasútüzemi érdekesség: a gyár területén kisvasúti hálózat található, melyet rendszeresen használnak a belső, üzemi szállításokhoz.
A vállalatnak saját üzemén kívül is komoly kapcsolata van a kisvasutakkal. A szobi pályafelújításhoz is Lábatlanban készítették a betonaljakat, és Debrecenben a Zsuzsivasút legkorszerűbb, betonaljas szakaszába is lábatlani aljakat építenek be.
A szerző köszönetet mond a cikk elkészítéséhez nyújtott, elengedhetetlen együttműködésért a Lábatlani Vasbetonipari Zrt.-nek. Külön köszönet a segítségért Váli Veronikának és Bogyó Tibornak, valamint köszönet a vállalat alkalmazottainak, hogy a fotózás során készségesek és együttműködők voltak.
Felhasznált irodalom:
A Lábatlani Vasbetonipari Zrt. weblapja és termékleírásai
MÁV D.54.sz. Építési és pályafenntartási műszaki adatok, előírások (Közdok)
MSZ 4710-1:1967, MSZ 4710-2:1967, MSZ 4710-3:1967 és MÁVSZ 2964 szabványok